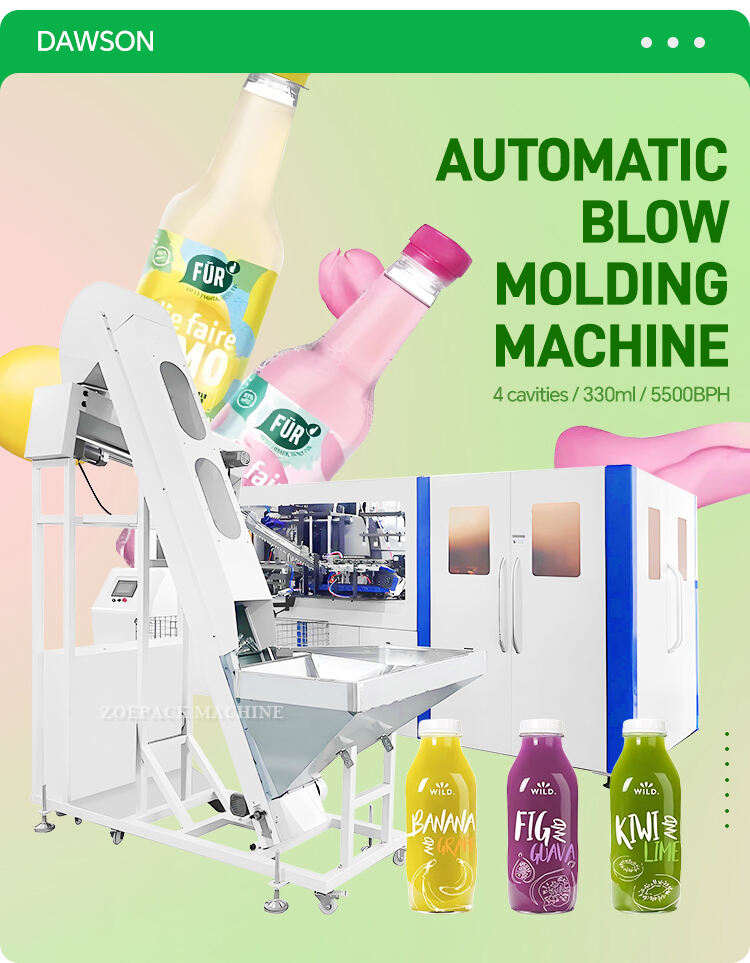
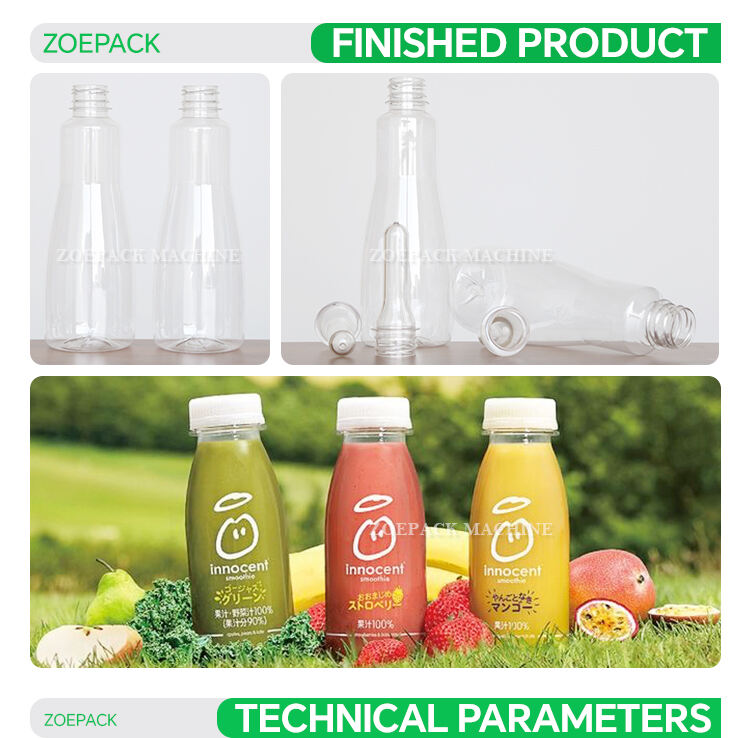
Preobrazite proizvodnjo bočic z našo polnoavtomatsko mašino za oblikovanje bočic s 4 jamnami
V hitro se spreminjajočem okolju proizvodnje plastikastih bočic so učinkovitost, natančnost in versatilnost temeljni kamen uspeha. Naša polnoavtomatska mašina za oblikovanje bočic s 4 jamnami pride kot rešitev, ki spremeni pravilo igre, ozretno inžinirana za izpolnitev različnih zahtev sodobne proizvodnje, hkrati pa določa nove standardne vrednosti v industriji.
Intuitivni dotikovni barvni sistem HMI za enostavno uporabo
V središju naše mašine za lepanje steklenic leži napreden dotikovni barvni sistem človek-štirijski vmesnik (HMI), ki ponovno določa uporabniško izkušnjo pri proizvodnji steklenic. Ta odlična vmesnika ponuja neprekinjeno in intuicijsko delovanje, kar jo dela dostopno za tako novice kot za izkušene operaterje. Sijajna barvana prikazna plošča omogoča jasno in stručno vizualno informacijo, kar omogoča operaterjem, da lahko spremlja in nadzira vsako stran proizvodnje z enostavno.
Z le-ti pripadajočimi dodatki na dotikovem zaslonu lahko operatorji enostavno nastavijo proizvodne parametre, kot so temperatura, tlak in čas cikla. Sistem HMI ponuja tudi odziv v realnem času o izvedbi stroja, kar omogoča operatorjem takojšnje prilagajanje za optimizacijo učinkovitosti proizvodnje. Bodisi se začne nova proizvodna serija, se spremeni oblika steklenice ali pa se rešuje težava, dotikov sistem HMI poenostavi celoten postopek, zmanjša krivuljo učenja in minimizira tveganje človeške napake. Ta uporabniški načrt ne le poveča proizvodnost, ampak tudi zagotavlja konstantno in visoko kakovost izhoda.
Impresiven kapacitet in neoporečna hitrost
Ena najbolj znamenkajnih lastnosti naše 4-otrošne polnoma avtomatske mašine za lepanje steklenic je njena izjemna zmogljivost in hitrost. Z možnostjo lepanja steklenic s maksimalnim prostorninom 10 litrov je ta stroj primern za širok obseg uporab, od majhnega embalovanja do proizvodnje v velikem obsegu. Ne glede na to, ali je potrebno proizvesti steklene posode za kuharsko olje, nealkoholne piče, mineralno vodo, vino, zdravila, kosmetiko ali katere koli druge tekočinske produkte, naš stroj jih lahko obravnava z enostavno.
Vse pa še ni konec. S maksimalno proizvodno hitrostjo 1500 embalazij na uro naša strojna oprema preseganja veliko konkurentov na trgu. Četrkova konstrukcija omogoča hkratno izdelavo več embalazij, kar značilno poveča izhod, ne da bi se pri tem zanemarila kakovost. Ta visokoteminska proizvodnja ne le skrati čase izdelave, ampak proizvajalcem omogoča, da izpolnjujejo strogim rokom in obsežnim naročilom z učinkovitostjo. Napredne avtomatske funkcije in natančni vmesni sistemi strojnega postrojenja zagotavljajo, da je vsaka embalacija proizvedena s stalno kakovostjo, neodvisno od hitrosti proizvodnje.
Neprezenčna versatilnost za različne uporabe
Naša 4-otrožna polna avtomatska mašina za lepanje butelj je zasnovana tako, da je zelo versatilna, kar jo dela idealnim izbirom za proizvajalce v različnih industrijskih področjih. Je združljiva s vsemi vrstami PET (Polietilen Tereftalat) butelj, ki so široko uporabljene pri pakiranju različnih izdelkov. Ali proizvajate hrbetne butelje za enkratne pijače ali težke posode za industrijske tekočine, naša mašina lahko z natančnostjo obdeluje različne oblike, velikosti in debeline sten butelj.
Gibanost mašine se razširja nad sami velikost in obliko butelj. Lahko tudi prilagaja različnim proizvodnim zahtevam, kot so različni proizvodni obsegi in proizvodni razpisi. S svojim hitro-spremenljivim sistemom form, lahko operatorji preprosto preklopujejo med različnimi oblikami butelj, kar omogoča hitro proizvodnjo prilagojenih butelj. Ta versatilnost omogoča proizvajalcem, da hitro rešijo tržne zahteve, izda novo produkcijo in ostanejo pred konkurencijo.
Precizno inženirstvo za vrhunsko kakovost
Kakovost je v srcu naše 4-kratne polnoma avtomatske aparature za lepanje steklenic. Vsak del stroja je natančno izdelan z uporabo najnovejše tehnologije in visokokakovostnih materialov, da se zagotovi zanesljiva in konzistentna delovanja. Napredna ekstruzijska sistema ravnomerno gredi in topi PET material, kar zagotavlja gladko in konstantno točen pretok plastike. To pomeni, da imajo stekline enakodebeljene zidne pladnje, odlično prosojnost in izjemno moč.
Postopek fižanskega lepanja je tudi pozornostno nadzorovan, da se zagotovi, da je vsaka butelja oblikovana z natančnostjo. Sistem visokega tlaka na stroju raztegne plastni parizon v želeno obliko z natančnostjo, ustvarjajoč butalje z gladkimi površinami in točnimi dimenzijami. Poleg tega je stroj opremljen s senzorji za kakovostni nadzor, ki spremljajo različne aspekte proizvodnje v realnem času. Če je zaznana kakršnakoli odstopanje od določenih parametrov, lahko stroj samodejno prilagodi ali ustavi proizvodnjo, da se prepreči izdelava poškodovanih izdelkov. Ta odločnost glede kakovosti zagotavlja, da vsaka butelja, ki jo proizvaja naš stroj, izpolnjuje najvišje industrijske standarde.
Dizajn z shranjevanjem energije in prijazen okolju
V današnji svetovni kulturi, ki je usmerjena v okolje, je trajnostnost eden od glavnih prednosti. Naša 4-otrožna polna avtomatska stroj za oblikovanje steklenic je načrtovana z lastnostmi, ki šteti energijo, kar ne le zmanjšuje stroške operacij, ampak tudi pomanjšuje vpliv na okolje. Inteligentni segrevni sistem stroja uporablja napredno tehnologijo nadzora temperature za optimizacijo porabe energije, tako da se material PET segreva na idealno temperaturo brez izgube presežne energije.
Učinkovit hlajni sistem igra tudi ključno vlogo pri štednji energije. Hitro hladi oblikovane steklenice, kar zmanjšuje skupno čas proizvodnje in še bolj šteti energijo. Z izbiro naše stroje za oblikovanje steklenic lahko proizvajalci prispevajo k zelenemu prihodnjejo, hkrati pa uživajo v znatnih štednjah na računih za energijo.
Popolna podpora po prodaji
Razumemo, da je vlaganje v novo proizvodno strojno opremo pomemben odločitev, in se zavezujemo, da bomo našim strankam zagotovili kompletne storitve podpore po prodaji. Naša ekipa izkušenih tehničarjev je na voljo za pomoč pri namestitvi, usposabljanju in ohranjanju, tako da bo vaš stroj vedno deloval z najvišjo učinkovitostjo.
Od trenutka, ko se vaš stroj pojavlja v vaši enoti, bodo naši strokovnjaki tesno sodelovali z vami, da se zagotovi gladki proces namestitve. Ponujamo globlja usposabljanja za vaše operaterje, ki pokrivajo vse od osnovnega delovanja do naprednega reševanja težav. Poleg tega ponujamo redna ohrabnavska storitva, da ohranimo stroj v optimalnem stanju, predaljšajoč njegovo uporabo in maksimirajojo njegovo proizvodnost. Naš odziviti tim strokovne podpore je vedno na voljo za reševanje vseh vaših težav ali vprašanj, zagotavljajoč hitre rešitve za minimizacijo neaktivnega časa.
V zaključku, naša 4 kave v celoti avtomatska mašina za lepanje steklenic predstavlja revolucionarno rešitev, ki ponuja neprimerljivo izvedbo, versatilnost in kakovost. S svojim intuitivnim dotikovim HMI sistemom, impresivno zmogljivostjo in hitrostjo, širokim obsegom uporabe, preciznim inženirstvom, energetsko učinkovitim dizajnom ter komprehensivno podporo po prodaji je idealen izbor za proizvajalce, ki iščejo povečanje zmogljivosti proizvodnje, izboljšanje kakovosti produkta in zmanjšanje stroškov. Ne izgubite priložnosti, da revolucionarizirate svoj proces proizvodnje steklenic – kontaktirajte nas danes in saznajte več o tem, kako lahko naša mašina spremeni vaš posel.
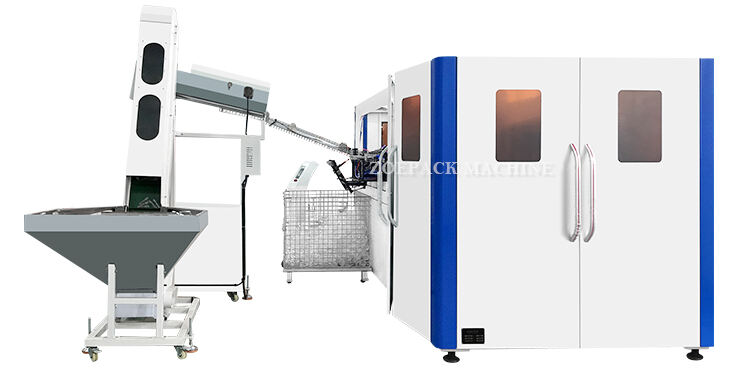
TehničniParametri |
ZPA-1L-2 |
ZPA-2L-2 |
ZPA-1L-4 |
ZPA-2L-4 |
ZPA-1L-6 |
ZPA-2L-6 |
|
Kamora |
2 |
2 |
4 |
4 |
6 |
6 |
Parameter glavnega stroja |
Sistem zaklepovanja |
35000 |
45000 |
48000 |
48000 |
56000 |
65000 |
Močna pot |
90 |
110 |
90 |
125 |
90 |
125 |
Pot raztegave |
300 |
400 |
260 |
330 |
260 |
330 |
Pot dnevnega držala |
50 |
50 |
50 |
50 |
50 |
50 |
Razmik med steklenicami |
76.2 |
114.3 |
76.2 |
114.3 |
76.2 |
114.3 |
Predoblika steklenice Številka |
66 |
52 |
95 |
82 |
106 |
92 |
Parametri izdelkov |
Maksimalna zmogljivost |
600 |
1500 |
600 |
1500 |
600 |
1500 |
Maksimalna višina telesa flaše |
260 |
330 |
260 |
330 |
260 |
330 |
Maksimalni premer telesa flaše |
68 |
105 |
68 |
105 |
68 |
105 |
Maksimalna višina predoblike flaše |
100 |
140 |
100 |
140 |
100 |
140 |
Maksimalna flaša Premer usma |
38 |
38 |
38 |
38 |
38 |
38 |
Električen Parametri |
Kapaciteta |
2500 |
2000 |
4500 |
4000 |
7200 |
6000 |
Količina greljenja v peči |
2*2 |
4*4 |
4*4 |
5*5 |
4*4 |
5*8 |
Količina topilnih lamp |
2*8 |
4*8 |
4*7 |
5*9 |
4*8 |
5*9 |
Ogrevanje Konfiguracija Moč |
32 |
48 |
42 |
72 |
64 |
90 |
Skupna močna zmogljivost |
36 |
50 |
45 |
80 |
69.5 |
100 |
Strojni napetost |
380V50HZ |
380V50HZ |
380V50HZ |
380V50HZ |
380V50HZ |
380V50HZ |
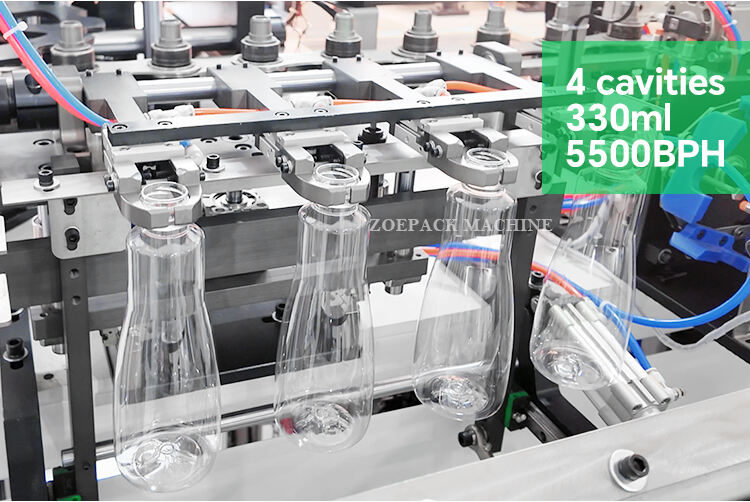
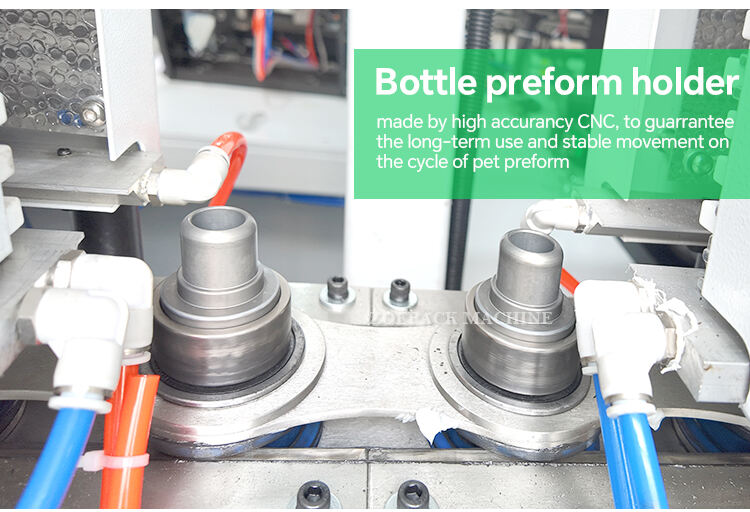
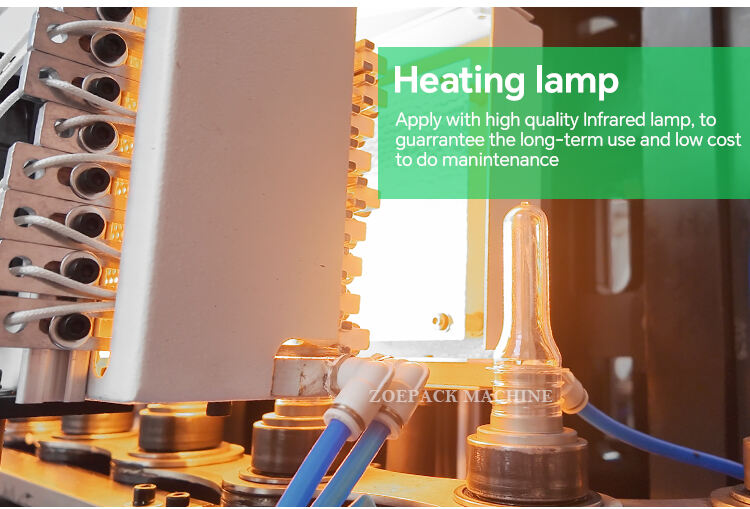
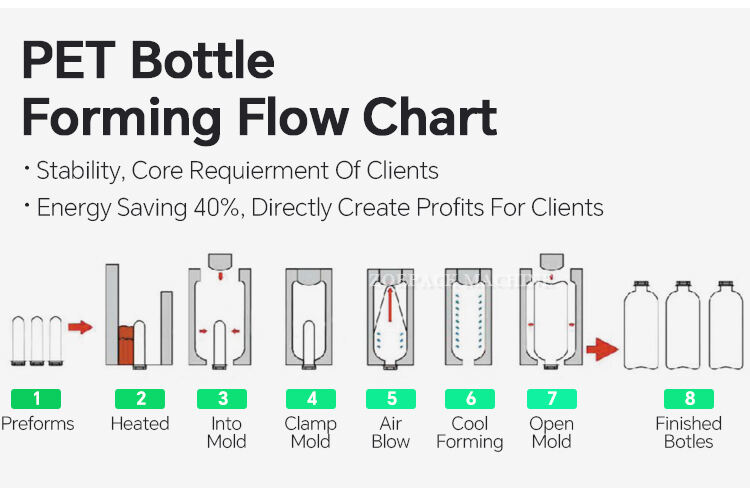
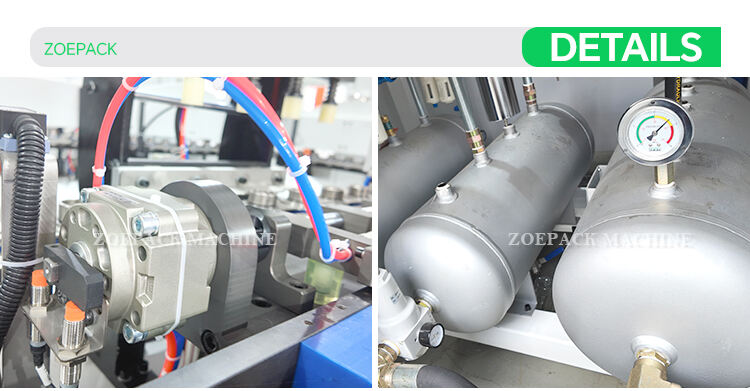
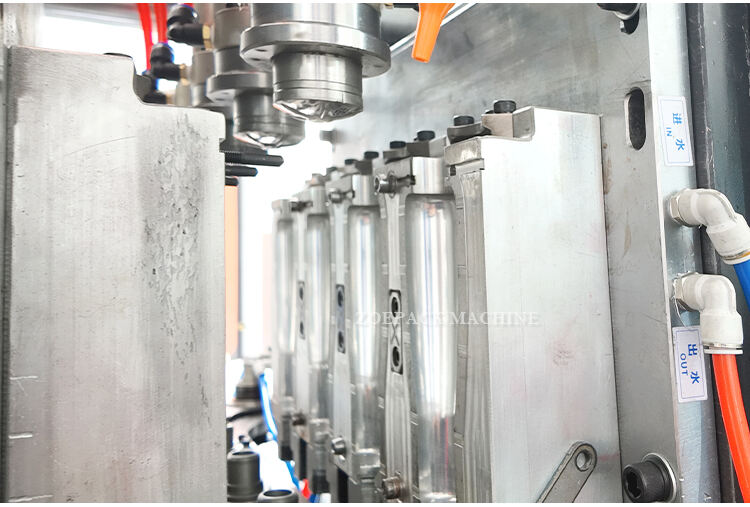
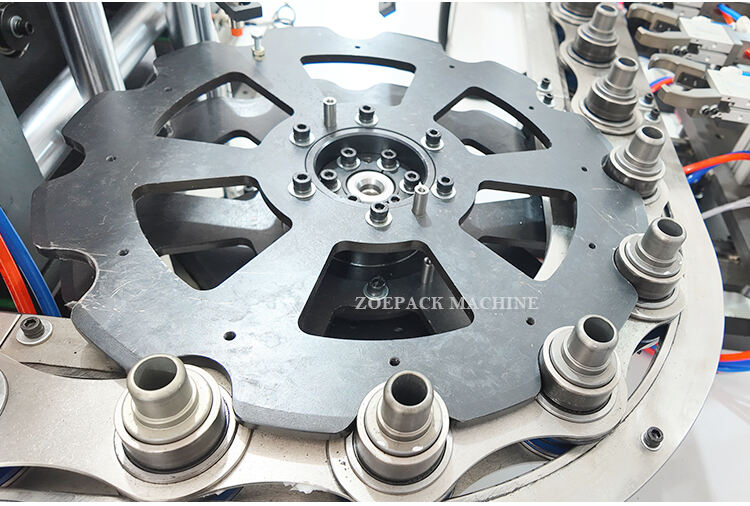
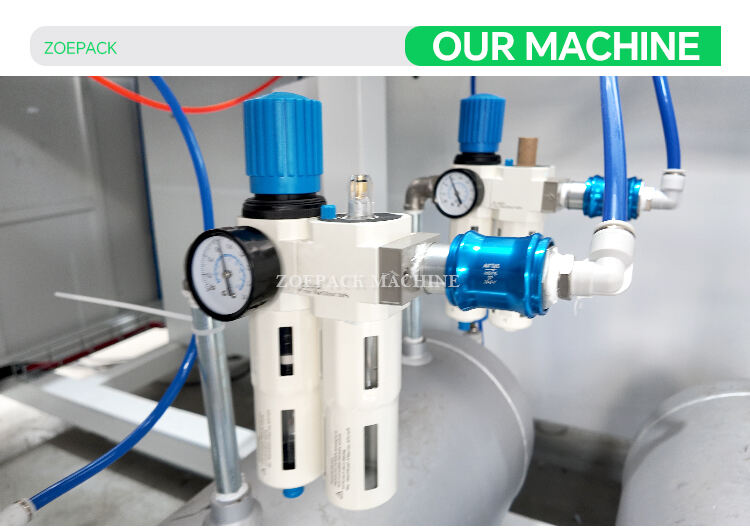
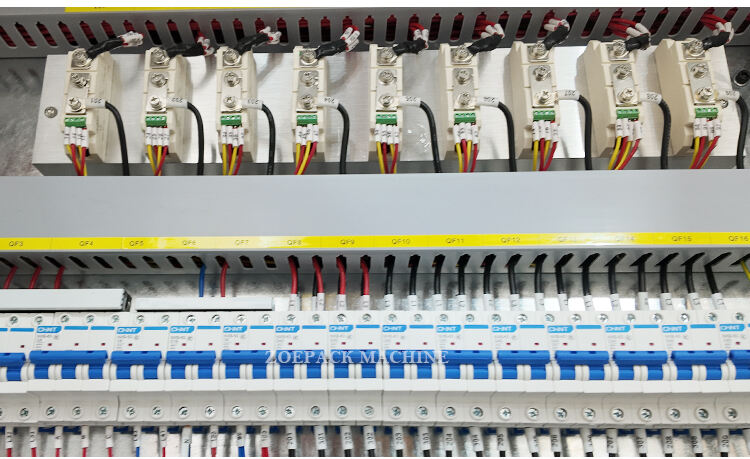
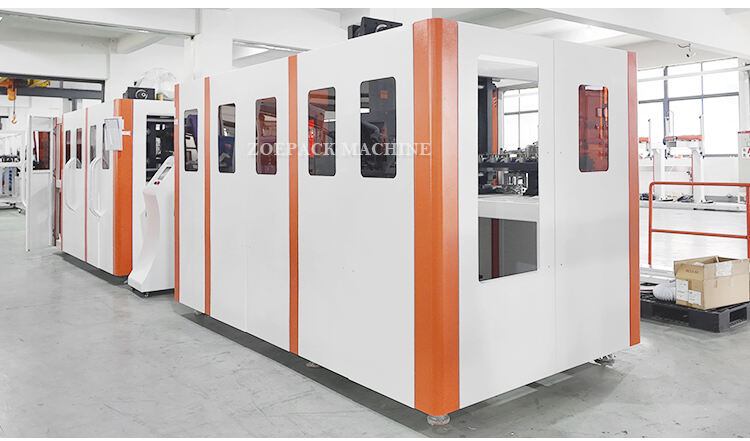
1. stabilno in točno delovanje pri visoki hitrosti, uporablja bolj stabilen in napreden mikrokompaktni PLC nadzorni sistem.
2. proizvodni postopek je popolnoma avtomatiziran, z prednostmi nizejega investicija, visoke učinkovitosti, enostavnega uporabe, preproste održave in varnosti.
3. primerni za fleksibilno proizvodnjo v večjih količinah ter različnih oblik bočkov, širok obseg uporabe, izpolnjuje potrebe strank.
4. ročne in avtomatske metode delovanja, nadzor človek-strojski vmesnik.
preprostim delovanjem.
5. sistem servoprevoza, visoka točnost postavitve, hitra stabilizacija hitrosti in dobra zanesljivost.
6. odpadni obremenitev manj kot 0,2 % za zaključeno stekleno buteljo.
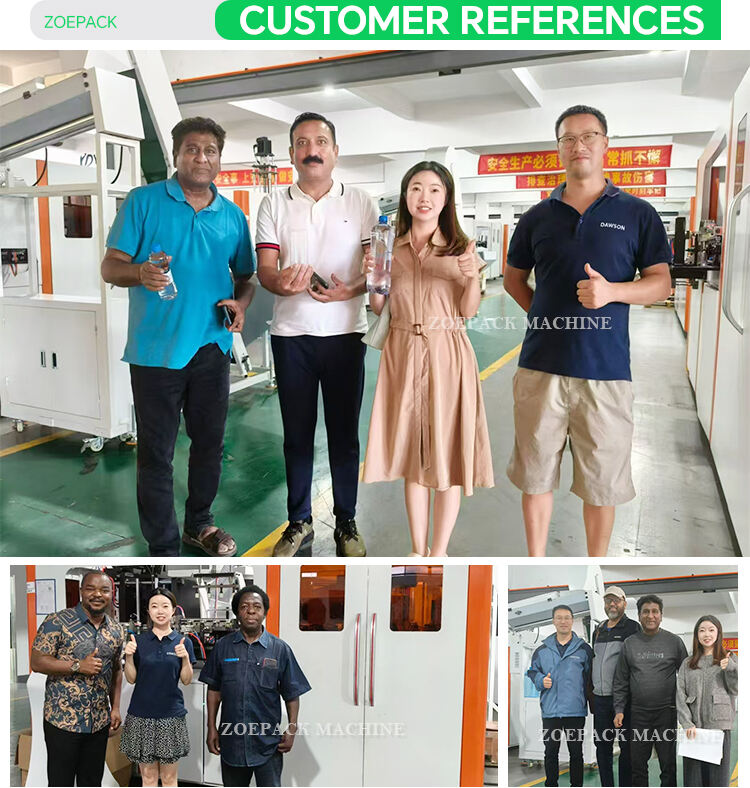
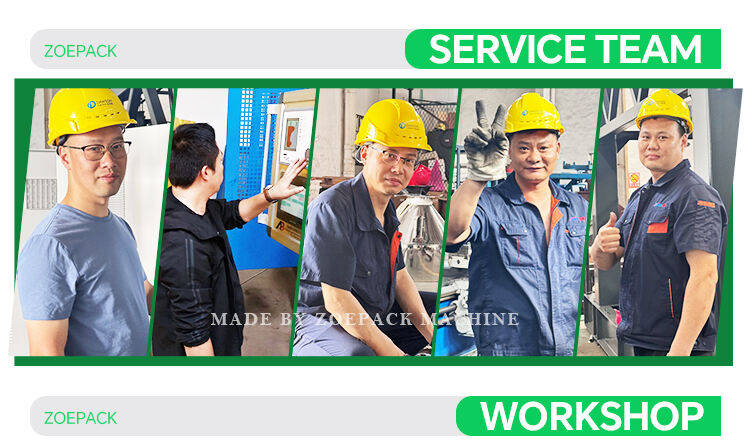
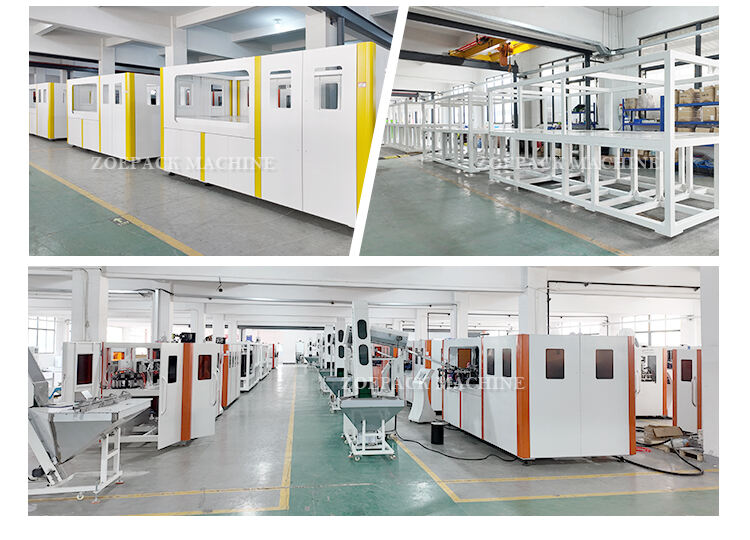
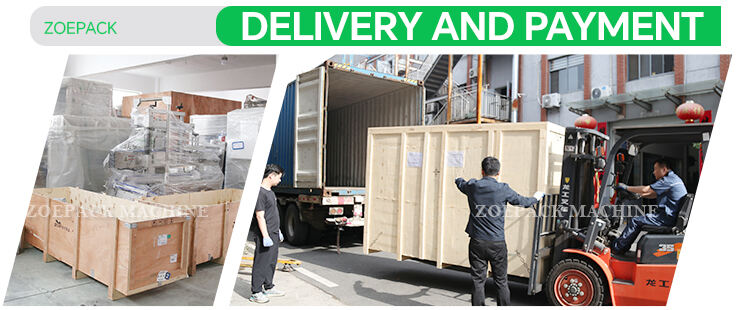
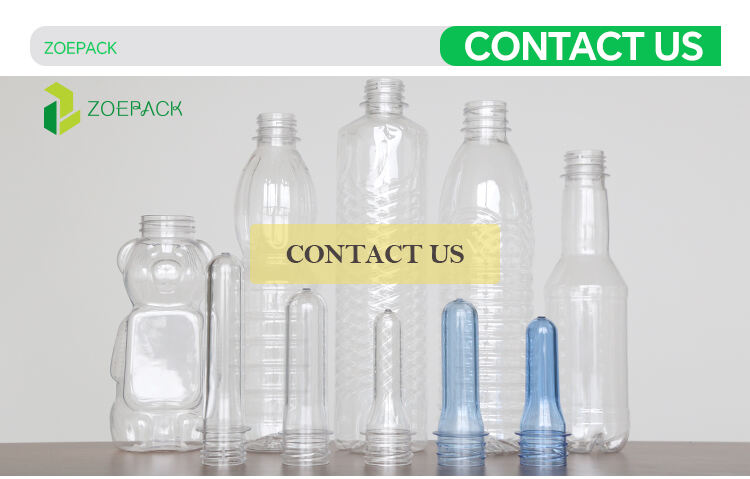